冻干工艺由冷冻和干燥(一次和二次)两个主要阶段构成,在干燥阶段,冻干机内部要创造一个真空环境,实现水或其他溶剂从产品中的升华和解吸,因此冻干机的主要构成部件箱体和冷阱及部分管路首先是要满足负压的设计。冻干机发生真空泄露,可能会对真空性能产生潜在影响,但如果真的发现泄露已经到达能影响设备抽空性能的程度,那么反倒应该恭喜,因为能抵消一定真空泵抽空能力的泄露缺陷,其实反而容易被找到,找到了也就容易被解决。更多的情况下,面对的是相对“微小”的泄露或多点微小泄露的叠加,这种泄露影响的是设备“密闭性/完整性”的指标:泄露率。对于无菌生产用途的冻干机,由于冻干机绝大部分机械密封面都坐落于非无菌/非定级的房间环境内,因此容器“密闭性”的缺陷有带来引入污染的可能,对保证内部无菌条件带来潜在的挑战,当然漏率和无菌风险评价不一定“直接”相关,之前也写过相关短文 《冻干机漏率合格=无菌保证?》,这里就不做赘述。然而寻找真空泄露点,尤其是微小泄露并不是一件轻松的事情。仍记得十几二十年前,自己在车间围着设备到处排查漏点的情形,那时最多采用是“排除法”,即将设备上的接口或管路逐一断开进行排查,确认哪个接口影响了漏率,不得不庆幸那时的设备结构也相对简单,“中奖”概率还是很高,不能与今日技术人员所面对工作量相比。即使这样,也会出现发现盲区,如同做统计时检查多次,仍遇到数值对不上的那种令人焦躁的情况。那么一些辅助手段就会被应用了,比如向或在存在密封面的地方,喷洒或涂抹一些挥发性好的物质,比如酒精,也有肥皂沫的…, 寄希望于挥发物通过泄漏点进入设备内部,从而导致真空变化,借此发现泄露缺陷。显然这种“经济”的方法有其局限性,首先默认泄露孔径足够让挥发物质进入设备腔体内,其次设备腔体内体积不太大,否则挥发量不足以带来可测量的影响。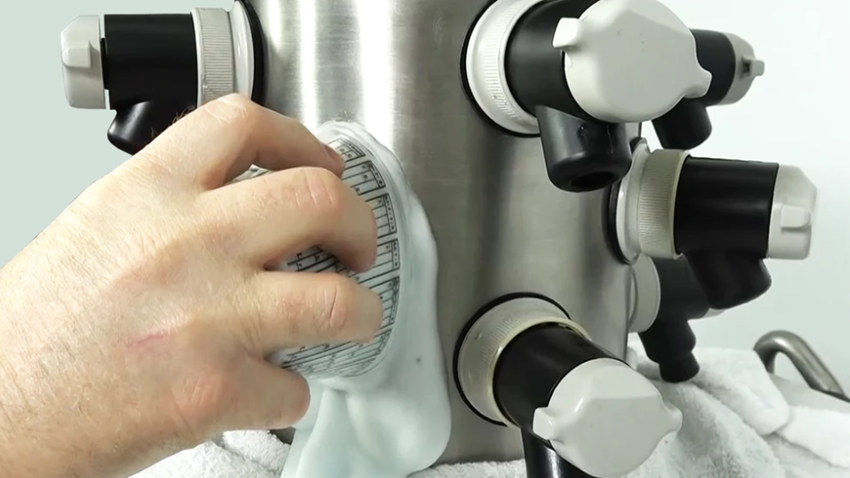
上面曾经历的两种检查泄漏点的方法虽然“朴素”,但其排障思路是如今仍可被借鉴的,首先,要熟悉设备的构造,这是所有trouble shooting的前提,要知道有哪些密封面会影响设备的真空性能,其一旦发生密封缺陷就会导致漏率不合格,并可以评估哪处密封的泄露概率更高,优先进行排查,提高效率。其次,对于难以发现的泄露,可使用探测精度更高的氦质谱检漏方法,虽然需要一定的投资,但收益也是明显的,其可以更有效和准确地定位缺陷。氦能够通过一些其它分子不能通过的狭缝以到达检测仪器。在真空环境中的氦气灵敏度约为5x10-12毫巴升/秒。氦气泄漏检测有很多不同的测试逻辑,可根据实际情况选用适合的方法,比如Spraying test。泄露率表明了真空设备是否具有良好的密封性(这里指的是基础”泄露Base/Real Leaks,而非“虚拟“泄露Virtual Leaks)。真空完整性测试是工厂验收测试(FAT)、现场验收测试(SAT)和/或运行确认(OQ),乃至整个设备使用生命周期内的重要工作内容。一旦发现设备漏率无法到达预先制定和曾实践的标准,那么应当对设备进行检查,找到导致泄露的设备缺陷并进行维护,不能简单的妥协。