常温:板层温度与灌装间环境温度接近或者略低,但不会低于露点温度以下,例如10-15°C。 低温:对于一些温度敏感的产品或需要速冻的剂型,会遇到考虑低于常温条件的设定,此时低温装载根据工艺要求,又分为低于露点温度(例如4-8°C)和低于霜点温度(低于0℃)两种情况。有些产品需要在很低温度下装载到预冷冻的板层上,甚至远低于0℃。比如低至-40°C,这有可能已经低于产品的关键温度,这就意味着,先装载上的产品会比后装载的产品会获得更多的冷冻时间。
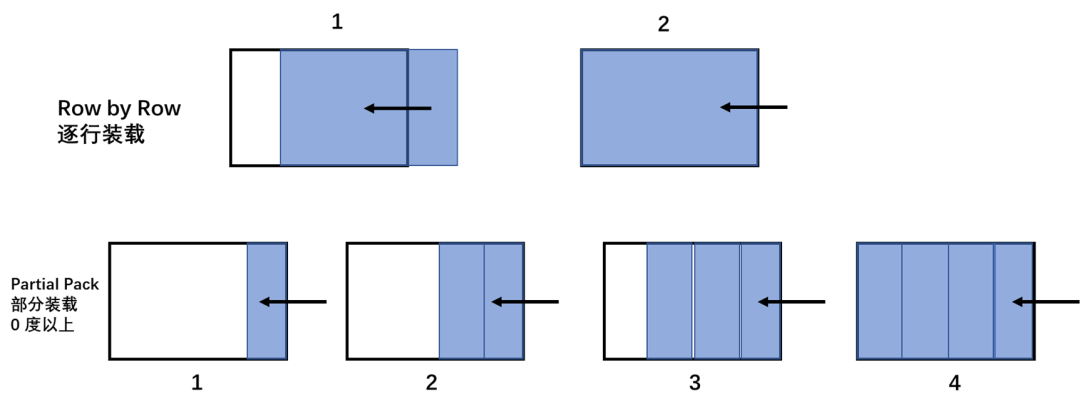

举报
提交
取消
为帮助审核人员更快处理,请填写举报原因:
评论
匿名
提交
取消
匿名
{{item_parent.created_at}}
置顶
批准
驳回
编辑
等待审核
已驳回
回复
{{item_parent.show_reply_list ? '收起回复' : '查看回复'}}({{item_parent.children.length}})
编辑
提交
取消
写回复
匿名
提交
取消
{{item_children.from_user}} 回复 {{item_children.to_user}}
{{item_children.created_at}}
批准
驳回
编辑
等待审核
已驳回
回复
编辑
提交
取消
写回复
匿名
提交
取消
举报
提交
取消
为帮助审核人员更快处理,请填写举报原因: